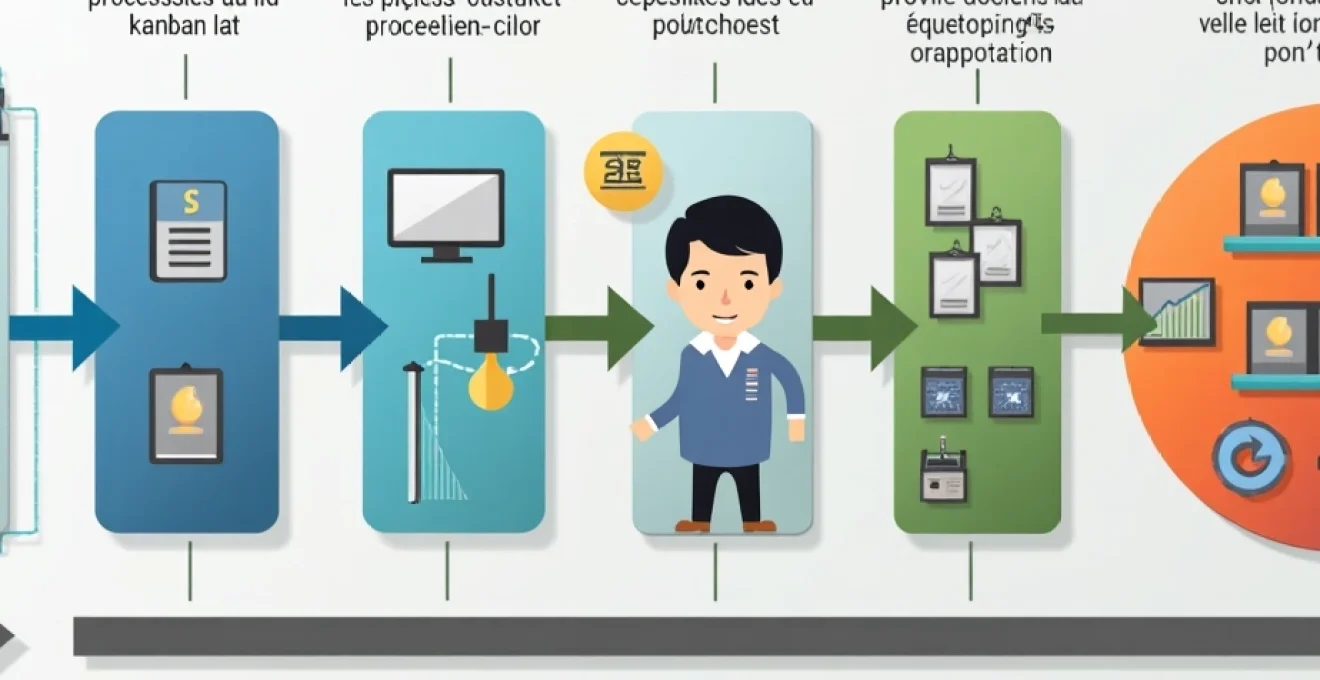
La gestion des flux en production représente un pilier fondamental dans l'optimisation des processus manufacturiers modernes. Cette approche, qui vise à synchroniser et rationaliser le mouvement des matériaux, des informations et des produits à travers la chaîne de valeur, est devenue incontournable pour les entreprises cherchant à maintenir leur compétitivité dans un marché globalisé. En mettant l'accent sur la réduction des gaspillages, l'amélioration de la qualité et la flexibilité opérationnelle, la gestion des flux transforme radicalement la manière dont les organisations conçoivent et exécutent leurs opérations de production.
Principes fondamentaux du flux tiré dans la gestion de production
Le concept de flux tiré, ou pull system , constitue l'un des principes clés de la gestion moderne des flux de production. Contrairement au système traditionnel de flux poussé, où la production est basée sur des prévisions, le flux tiré répond directement à la demande réelle du client. Cette approche permet de réduire considérablement les stocks excédentaires et d'améliorer la réactivité de la chaîne de production.
Dans un système de flux tiré, chaque étape du processus de production ne démarre que lorsqu'elle reçoit un signal de l'étape suivante, indiquant un besoin réel. Ce signal peut prendre diverses formes, mais la plus connue est sans doute le système Kanban. Cette méthode de gestion visuelle utilise des cartes ou des signaux électroniques pour déclencher la production ou le réapprovisionnement des matériaux uniquement lorsque c'est nécessaire.
L'adoption du flux tiré présente plusieurs avantages significatifs. Tout d'abord, elle permet une réduction drastique des stocks intermédiaires, libérant ainsi du capital et de l'espace de stockage. De plus, elle favorise une détection plus rapide des problèmes de qualité, car les lots de production sont généralement plus petits et les défauts sont identifiés plus tôt dans le processus. Enfin, cette approche améliore la flexibilité de la production, permettant aux entreprises de s'adapter plus rapidement aux fluctuations de la demande.
Le flux tiré transforme la production d'un système basé sur les prévisions à un système réactif guidé par la demande réelle, optimisant ainsi l'utilisation des ressources et la satisfaction client.
Optimisation des processus avec le système kanban
Le système Kanban, développé par Taiichi Ohno chez Toyota dans les années 1950, est devenu un outil incontournable dans la gestion des flux de production. Son nom, qui signifie "carte" ou "signal visuel" en japonais, reflète parfaitement son principe de fonctionnement. Le Kanban utilise des signaux visuels pour gérer le flux de matériaux et d'informations dans un système de production, assurant que les pièces sont produites et livrées juste à temps pour leur utilisation.
Mise en place des cartes kanban physiques et électroniques
La mise en œuvre du système Kanban peut se faire à travers des cartes physiques ou des systèmes électroniques. Les cartes Kanban physiques sont des outils visuels simples mais efficaces, souvent attachées aux conteneurs de pièces. Elles contiennent des informations essentielles telles que la référence de la pièce, la quantité, l'emplacement de stockage et le point de réapprovisionnement.
Les systèmes Kanban électroniques, quant à eux, utilisent des technologies numériques pour transmettre les signaux de production. Ces systèmes offrent l'avantage d'une mise à jour en temps réel et d'une intégration plus facile avec les systèmes d'information de l'entreprise. Ils permettent également une meilleure traçabilité et une analyse plus approfondie des flux de production.
Calcul et ajustement des tailles de lots kanban
Le calcul de la taille optimale des lots Kanban est crucial pour l'efficacité du système. La formule de base pour déterminer le nombre de Kanbans nécessaires est :
Nombre de Kanbans = (Demande journalière x Temps de réapprovisionnement x (1 + Facteur de sécurité)) / Taille du conteneur
Cependant, cette formule n'est qu'un point de départ. L'ajustement continu des tailles de lots est essentiel pour maintenir l'efficacité du système face aux changements de la demande ou des conditions de production. Une approche courante consiste à réduire progressivement le nombre de Kanbans pour identifier et résoudre les problèmes de processus, une technique connue sous le nom de "réduction Kanban".
Gestion des flux avec le tableau heijunka
Le tableau Heijunka, ou boîte de nivellement, est un outil complémentaire au système Kanban qui vise à lisser la production en répartissant uniformément le volume et la variété des produits sur une période donnée. Ce tableau visuel permet de planifier la production de manière à éviter les pics et les creux, réduisant ainsi le stress sur les ressources de production et améliorant la stabilité du flux.
L'utilisation du tableau Heijunka implique de diviser la production en intervalles de temps réguliers et d'allouer les cartes Kanban à ces intervalles de manière équilibrée. Cette approche aide à minimiser les stocks tout en assurant une réponse régulière à la demande client, même lorsque celle-ci fluctue.
Intégration du kanban dans les ERP comme SAP et oracle
L'intégration du système Kanban dans les progiciels de gestion intégrés (ERP) comme SAP et Oracle représente une évolution significative dans la gestion des flux de production. Ces intégrations permettent de combiner la simplicité et l'efficacité du Kanban avec la puissance de traitement et d'analyse des ERP.
Dans SAP, par exemple, le module de gestion Kanban permet de configurer et de gérer des cycles Kanban électroniques, de suivre les mouvements de stock en temps réel et d'automatiser les processus de réapprovisionnement. Oracle offre des fonctionnalités similaires, permettant une gestion fine des flux de production basée sur les principes du Kanban.
Cette intégration facilite non seulement la gestion quotidienne des flux, mais permet également une analyse plus approfondie des performances, aidant ainsi à identifier les opportunités d'amélioration continue dans le processus de production.
Techniques de lissage de la production
Le lissage de la production, ou production leveling , est une technique essentielle dans la gestion des flux qui vise à réduire les variations et les irrégularités dans le processus de production. Cette approche permet d'optimiser l'utilisation des ressources, de réduire les temps d'attente et d'améliorer la qualité globale de la production.
Application du takt time pour synchroniser la production
Le Takt time, terme dérivé de l'allemand signifiant "rythme" ou "cadence", est un concept crucial dans le lissage de la production. Il représente le rythme de production nécessaire pour répondre exactement à la demande client. Le calcul du Takt time se fait en divisant le temps de production disponible par la demande client pour cette période :
Takt time = Temps de production disponible / Demande client
L'application du Takt time permet de synchroniser toutes les étapes de la production sur un rythme commun, aligné sur la demande réelle. Cette synchronisation aide à identifier rapidement les goulots d'étranglement et les inefficacités dans le processus de production. De plus, elle favorise un flux continu et régulier, réduisant ainsi les stocks intermédiaires et les temps d'attente.
Mise en œuvre du SMED pour réduire les temps de changement
Le SMED (Single-Minute Exchange of Die), ou changement rapide d'outil, est une technique développée par Shigeo Shingo pour réduire drastiquement les temps de changement entre deux productions. Cette méthode est essentielle pour permettre une production flexible et réactive, capable de s'adapter rapidement aux changements de la demande.
La mise en œuvre du SMED implique plusieurs étapes :
- Identifier et séparer les opérations internes (qui nécessitent l'arrêt de la machine) des opérations externes
- Convertir autant d'opérations internes que possible en opérations externes
- Rationaliser toutes les opérations restantes
- Standardiser et documenter le nouveau processus
En réduisant les temps de changement, le SMED permet de produire en lots plus petits sans perte d'efficacité, facilitant ainsi l'adoption d'un système de production tiré et flexible.
Utilisation du Poka-Yoke pour prévenir les erreurs de flux
Le Poka-Yoke, terme japonais signifiant "prévention des erreurs", est une approche visant à concevoir des processus et des outils qui rendent les erreurs pratiquement impossibles. Dans le contexte de la gestion des flux, le Poka-Yoke joue un rôle crucial en assurant la qualité et la régularité du flux de production.
Les dispositifs Poka-Yoke peuvent prendre diverses formes, allant de simples guides physiques à des systèmes électroniques sophistiqués. Par exemple, un connecteur qui ne peut être inséré que dans le bon sens, ou un système de détection automatique qui arrête la ligne de production en cas d'anomalie. Ces dispositifs permettent non seulement de prévenir les erreurs, mais aussi de les détecter immédiatement lorsqu'elles se produisent, minimisant ainsi leur impact sur le flux de production.
L'intégration du Poka-Yoke dans la gestion des flux transforme la prévention des erreurs d'une responsabilité individuelle à une caractéristique intrinsèque du processus, garantissant ainsi une qualité constante et un flux ininterrompu.
Implémentation du value stream mapping dans la gestion des flux
Le Value Stream Mapping (VSM), ou cartographie de la chaîne de valeur, est un outil puissant pour visualiser et optimiser les flux de production. Cette technique permet de représenter graphiquement toutes les étapes impliquées dans le flux des matériaux et des informations nécessaires pour amener un produit du fournisseur au client. Le VSM est particulièrement efficace pour identifier les gaspillages et les opportunités d'amélioration dans le processus de production.
Cartographie de l'état actuel des flux de production
La première étape du VSM consiste à cartographier l'état actuel des flux de production. Ce processus implique de suivre le parcours d'un produit du début à la fin, en notant chaque étape, les temps de cycle, les temps d'attente, les niveaux de stock, et les flux d'information. Cette cartographie détaillée permet de visualiser clairement où se trouvent les inefficacités et les goulots d'étranglement dans le processus actuel.
Pour réaliser une cartographie efficace, il est essentiel d'impliquer des représentants de tous les départements concernés et de collecter des données précises sur le terrain. L'utilisation de symboles standardisés pour représenter les différents éléments du flux (comme les processus, les stocks, les transports) aide à créer une représentation claire et compréhensible pour tous les acteurs impliqués.
Identification des gaspillages avec la méthode des 7 muda
Une fois la cartographie de l'état actuel réalisée, l'étape suivante consiste à identifier les gaspillages dans le processus. La méthode des 7 Muda, développée dans le cadre du système de production Toyota, offre un cadre efficace pour cette analyse. Les 7 Muda, ou gaspillages, sont :
- Surproduction
- Attentes
- Transports inutiles
- Traitements inutiles ou mal faits
- Stocks excessifs
- Mouvements inutiles
- Défauts
En examinant chaque étape du flux à travers le prisme des 7 Muda, il devient possible d'identifier systématiquement les zones où la valeur n'est pas ajoutée et où des améliorations peuvent être apportées. Cette analyse approfondie est cruciale pour optimiser le flux de production et éliminer les activités qui ne contribuent pas directement à la valeur pour le client.
Conception de l'état futur optimisé des flux
Après avoir identifié les gaspillages et les inefficacités dans l'état actuel, l'étape suivante consiste à concevoir un état futur optimisé des flux. Cette phase implique de repenser le processus pour éliminer les gaspillages identifiés et créer un flux plus fluide et plus efficace.
La conception de l'état futur doit prendre en compte plusieurs éléments clés :
- L'introduction de flux tirés là où c'est possible
- La réduction des temps de cycle et des temps d'attente
- L'équilibrage de la charge de travail entre les différentes étapes
- L'optimisation des niveaux de stock
- L'amélioration de la communication et des flux d'information
L'objectif est de créer un flux continu, où chaque étape produit exactement ce dont l'étape suivante a besoin, quand elle en a besoin, réduisant ainsi les stocks intermédiaires et les temps d'attente.
Utilisation de logiciels comme microsoft visio pour le VSM
La réalisation d'un Value Stream Mapping peut être grandement facilitée par l'utilisation de logiciels spécialisés. Microsoft Visio, par exemple, offre des fonctionnalités spécifiques pour la création de VSM, avec des symboles préconçus et des modèles adaptés. Ces outils permettent non seulement de créer des représentations visuelles claires et professionnelles, mais aussi de manipuler facilement les données et de simuler différents scénarios.
L'utilisation de logiciels pour le VSM présente plusieurs avantages :
- Facilité de mise à jour et de modification des cartes
Bien que ces outils facilitent grandement le processus de création et d'analyse du VSM, il est important de se rappeler que la valeur réelle du VSM réside dans la réflexion et l'analyse qui l'accompagnent, plutôt que dans la simple création d'un diagramme esthétique.
Technologies avancées pour la gestion des flux de production
L'évolution rapide des technologies numériques offre de nouvelles opportunités pour optimiser la gestion des flux de production. Ces innovations permettent une visibilité accrue, une prise de décision plus rapide et une flexibilité améliorée dans les processus de fabrication.
Intégration de l'IoT industriel pour le suivi en temps réel
L'Internet des Objets Industriel (IIoT) révolutionne la gestion des flux de production en permettant un suivi en temps réel de chaque élément du processus de fabrication. Des capteurs connectés peuvent être installés sur les machines, les outils et même les produits en cours de fabrication, fournissant un flux constant de données sur leur état, leur performance et leur localisation.
Cette connectivité permet :
- Une visibilité en temps réel sur l'état de la production
- La détection précoce des anomalies et des goulots d'étranglement
- L'optimisation dynamique des flux basée sur les conditions réelles
- Une maintenance prédictive réduisant les temps d'arrêt imprévus
Par exemple, dans une usine automobile, des capteurs IoT peuvent suivre chaque véhicule tout au long de la chaîne de montage, permettant une coordination précise des approvisionnements et une personnalisation en temps réel selon les spécifications du client.
Utilisation de l'intelligence artificielle pour la prévision des flux
L'intelligence artificielle (IA) et le machine learning apportent une dimension prédictive puissante à la gestion des flux de production. En analysant de vastes quantités de données historiques et en temps réel, les algorithmes d'IA peuvent prévoir avec précision les tendances de la demande, les besoins en ressources et les potentiels problèmes de production.
Les applications de l'IA dans la gestion des flux incluent :
- La prévision précise de la demande pour optimiser les niveaux de stock
- L'anticipation des pannes machines pour une maintenance proactive
- L'optimisation dynamique des itinéraires de production
- L'ajustement automatique des paramètres de production pour maximiser l'efficacité
Par exemple, une entreprise de produits électroniques peut utiliser l'IA pour prédire les pics de demande saisonniers et ajuster automatiquement ses flux de production en conséquence, assurant ainsi une disponibilité optimale des produits tout en minimisant les stocks excédentaires.
Mise en place de jumeaux numériques pour simuler les flux
Les jumeaux numériques représentent une avancée significative dans la modélisation et la simulation des flux de production. Un jumeau numérique est une réplique virtuelle d'un système physique, qui peut être utilisée pour simuler, analyser et optimiser les processus de production en temps réel.
Les avantages des jumeaux numériques pour la gestion des flux incluent :
- La capacité à tester des scénarios "what-if" sans perturber la production réelle
- L'optimisation continue des flux basée sur des données en temps réel
- La détection précoce des inefficacités et des goulots d'étranglement potentiels
- La formation et la planification améliorées pour les opérateurs et les gestionnaires
Par exemple, un fabricant d'électroménager peut utiliser un jumeau numérique de sa ligne de production pour simuler l'introduction d'un nouveau modèle de réfrigérateur, identifiant ainsi les ajustements nécessaires dans les flux de production avant même le début de la fabrication réelle.
Mesure et amélioration continue des performances des flux
La mesure et l'amélioration continue des performances sont essentielles pour maintenir l'efficacité des flux de production dans un environnement en constante évolution. Cette approche systématique permet d'identifier rapidement les écarts par rapport aux objectifs et de mettre en œuvre des actions correctives ciblées.
Analyse des KPI de flux avec des outils comme tableau ou power BI
Les outils de Business Intelligence comme Tableau ou Power BI offrent des capacités puissantes pour analyser et visualiser les indicateurs clés de performance (KPI) liés aux flux de production. Ces plateformes permettent de créer des tableaux de bord interactifs et des rapports dynamiques qui offrent une vue d'ensemble claire des performances des flux.
Quelques KPI essentiels à suivre incluent :
- Temps de cycle
- Taux de rendement global (TRG)
- Niveau de stocks
- Taux de qualité
- Temps de changement de série
L'utilisation de ces outils permet non seulement de suivre ces KPI en temps réel, mais aussi d'effectuer des analyses approfondies pour identifier les tendances, les corrélations et les opportunités d'amélioration. Par exemple, un fabricant de composants électroniques pourrait utiliser Power BI pour créer un tableau de bord montrant l'évolution du temps de cycle sur différentes lignes de production, permettant ainsi d'identifier rapidement les zones nécessitant une optimisation.
Application de la méthode six sigma DMAIC aux flux de production
La méthode Six Sigma DMAIC (Define, Measure, Analyze, Improve, Control) offre un cadre structuré pour l'amélioration continue des flux de production. Cette approche systématique permet d'identifier et d'éliminer les causes de variation dans les processus, améliorant ainsi la qualité et l'efficacité des flux.
Les étapes du DMAIC appliquées aux flux de production sont :
- Définir : Identifier clairement le problème ou l'opportunité d'amélioration dans le flux
- Mesurer : Collecter des données précises sur les performances actuelles du flux
- Analyser : Utiliser des outils statistiques pour identifier les causes profondes des inefficacités
- Améliorer : Développer et mettre en œuvre des solutions pour optimiser le flux
- Contrôler : Mettre en place des mécanismes pour maintenir les améliorations à long terme
Par exemple, une entreprise de fabrication de pièces automobiles pourrait appliquer la méthode DMAIC pour réduire le temps de changement d'outil sur une ligne de production critique, augmentant ainsi la flexibilité et la réactivité de ses flux de production.
Mise en place de chantiers kaizen pour optimiser les flux localement
Les chantiers Kaizen, issus de la philosophie d'amélioration continue japonaise, sont des initiatives à court terme visant à optimiser rapidement des aspects spécifiques des flux de production. Ces événements concentrés, généralement d'une durée de 3 à 5 jours, rassemblent des équipes multidisciplinaires pour analyser, proposer et mettre en œuvre des améliorations immédiates.
Les avantages des chantiers Kaizen pour l'optimisation des flux incluent :
- Des résultats rapides et visibles
- Une implication directe des opérateurs dans le processus d'amélioration
- Une approche pragmatique et orientée vers l'action
- Le développement d'une culture d'amélioration continue
Par exemple, un chantier Kaizen pourrait être organisé pour optimiser le flux de matériaux dans une zone spécifique de l'usine, en réorganisant le layout, en mettant en place des systèmes visuels de gestion des stocks, et en standardisant les procédures de travail. Ces améliorations locales, une fois multipliées à travers l'ensemble de l'usine, peuvent conduire à des gains significatifs dans l'efficacité globale des flux de production.
L'amélioration continue des flux de production n'est pas simplement une série de projets isolés, mais une philosophie intégrée qui imprègne toute l'organisation, transformant chaque défi en une opportunité d'optimisation et d'innovation.